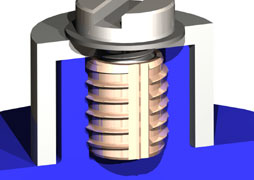
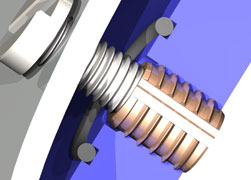
High performance threaded inserts for plastics
The Tappex Trisert® range of threaded inserts for plastics has been developed for various environments and application criteria post-mould installed. It includes three primary designs– double ended, reduced headed and headed, all available as normal and close-limit variants; lengths normally stated in mm.
Trisert®– Double ended- Product features
Three primary and three secondary equidistant cutting flutes over the length of the external form, give a more balanced cutting load than other forms of self-tapping insert (sometimes called: ‘self-threading’). The cutting action takes place at a larger number of points on the thread form over the length and circumference of the insert.
Lead-in feature on both ends allows the insert to be installed either way up which facilitates ease of handling. Therefore, where the volumes dictate that bowl feeding equipment is required, for example, it is not necessary to incorporate complex flighting or routing-systems to orientate the insert which makes bowl feeding simpler and reduces overall process-tooling costs.
Free running internal thread due to there being no interruption to the internal thread, as the external longitudinal flutes produce the cutting action during installation.
Reduced outward stress – during the installation process the cutting action of self-tapping inserts results in slight outward stress. This is reduced to an absolute minimum with the Trisert® and enables the insert to be used in more brittle materials and also where there are thin wall-sections.
Improved axial alignment – the balanced cutting load of the Trisert® reduces side thrust often caused by if only one cutting edge is available. Overall, this has the effect of guaranteeing much closer axial alignment of the insert in the hole.
Trisert®– Double ended – Design aids
- In conjunction with the three cutting flutes, greater interference can be achieved by the special truncated thread form increasing radial and pull out performance. Due to the Trisert’s coarse external thread form this retains a greater proportion of the predominantly weaker parent material and so improving the performance of the insert. This often allows shorter standard lengths to be specified
- The Trisert® is available in three standard lengths – short length for applications where space is limited, regular length, and long length for maximum pull out loading in all applications
- Due to the Trisert’s coarse thread form, the greater helix angle of the thread produces a greater resistant component of force radially, and as a consequence, this increases the radial stripping torque of the insert. It is possible to stall torque the Trisert® at the bottom of the hole increasing the locking action for applications subject to vibration
- One of the disadvantages of the slotted design of some self-tapping inserts is that the accumulation of swarf at the bottom of the insert can cause contamination of the insert’s internal thread. The Trisert® eliminates this problem as the majority of loose material is trapped in the cutting flutes
- Trisert® Advanced should be specified where thermoset materials are required as the interference between insert and component must be tightly controlled
- The Trisert® is a perfect cylinder i.e. it has not been weakened by a transverse slot or hole(s) and therefore it’s inherently stronger than many competing products and not likely to collapse when being installed into hard or abrasive materials. This also means that the Trisert® can be produced in smaller diameters and extends the range of potential applications to include those in reduced diameter moulded-bosses, thinner-wall sections and where space is limited
Trisert®– Reduced headed – Product features
The reduced headed version of the Trisert® incorporates the same special truncated thread form containing three primary and three secondary equidistant cutting flutes, but provides the designer and production engineer with a higher performance flush fitting insert to match product availability to common assembly problems. Reduced head at the same diameter as the external truncated thread form provides an increased bearing surface.
Trisert®– Reduced headed- Design aids
- It should be specified where a flush-fit finish is required
- It should be specified where higher tightening torques are required
- The head helps to prevent ‘jack out’ where elongated slots or slightly oversize holes are necessary in mating components
Trisert®– Headed- Product features
The headed version of the Trisert® incorporates the same special truncated thread form containing three equidistant cutting flutes, but provides the designer and production engineer with standard options to match product availability to common assembly problems. Large diameter head prevents jack out in applications where elongated slots or larger than standard clearance holes are necessary in the mating component. It has a larger bearing surface that is required in high torque applications.
Trisert®– Headed Design aids
- It should be specified in applications where increased resistance to rotation is required
- It also provides an excellent conductive surface for electrical contacts, ring connectors or eyelets
- The large head diameter helps to prevent ‘jack out’ in applications where elongated slots or larger than standard clearance holes are necessary in mating components
Trisert® Installation- FlexiArm®
The Tappex Trisert® can be installed using our specifically designed Tappex FlexiArm®, 035 series used in conjunction with our production drivers (029 series), with either Electrically (new range , available Q3 – 2019) or Pneumatically-actuated torque settable screwdrivers which provides a method of accurately installing inserts at various heights and positions in a moulding.
Click the videos tab to see the FlexiArm® in use or check-out our videos on You Tube.
Alternatively, Tappex Trisert® inserts, in low quantities, can be installed by hand quite efficiently using our 031 range of hand installation tools that come complete with alignment bushes to aid inserts being installed perpendicular to the work piece of substrate’s surface. Please contact our applications department for further information and details.
We have also recently released our newest installation tool for threaded inserts, the ElecArm, a series of electric preset-torque screwdrivers mounted on balance arms, and can be used in conjunction with a Tappex production driver (part no.029).
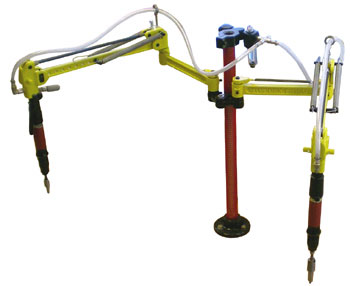
TRISERT® - DOUBLE ENDED - 145M2
REACH/RoHS compliant as per the candidate list of substances of very high concern.
Finish: Self-Colour. Special finishes to customer requirements, at extra cost.
Description: The Trisert is a self-tapping insert. Its main feature is a truncated external thread form with three equidistant main and three secondary cutting flutes.
Application: Offers higher tightening torque's and increased bearing surface for use with softer mating components. Use where a flush fit is required. Trisert Advanced should be specified for thin walls, hard Urea, Melamine and Phenolic materials or similar.
Hole Size: Moulded and drilled hole diameters vary dependent upon installation technique, specific component geometry and plastic material. Please consult our technical department for a precise recommendation, to ensure optimum production conditions. Sizes given are for reference purposes only.
Hole Design: The hole design information is intended to indicate the approximate dimensional requirements for satisfactory installation of the insert. They should not be specified for production tooling without prior consultation with our Application Engineering Department - we accept no responsibility should the use of this information without consultation result in product failure. Please call our application engineers for assistance +44 (0) 1789 206600
Installation: Self-tapping using a hand tool (part no.031) or reversible drive mechanism. Tappex offer pneumatic reversible tools mounted in a Tappex FlexiArm, used in conjunction with a Tappex production driver (part no.029).
We have also recently released our newest installation tool for threaded inserts, the ElecArm, a series of electric preset-torque screwdrivers mounted on balance arms, and can be used in conjunction with a Tappex production driver (part no.029).
Hole Design
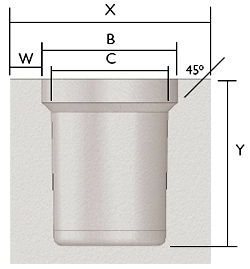
Boss Diameter X: | 5.80 mm |
Hole Depth Y: | 4.40 mm |
Hole Diameter C: | 3.10 mm-3.30 mm |
Wall Thickness W: | 1.25 mm |
Insert Design
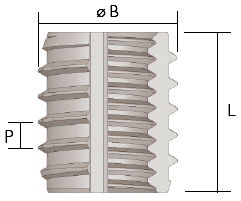
Diameter (external) B: | 3.50 mm |
Length L: | 4.00 mm |
Part No.: | 145M2 |
Pitch (external) P: | 0.79 mm |
Pitch (internal): | 0.4 |
Thread Size: | M2 |
The following are downloads relating to the Trisert® range, although a downloads may also be applicable to other product ranges. General information can be found on our downloads page.
If you can’t find what you are looking for, why not try our chat facility where one of our helpful team can assist you or simply give us a ring on +44 (0) 1789 206600.
Product brochure with overviews and descriptions of products.
Threaded Inserts for Plastics a ten point guide
Method of installing Triserts under Test conditions
Features and Description of the Tappex FlexiArm
Details of Production Driver Function, Identification, Dimensions, Suggested stock, and Troubleshooting.
Tappex Hand Tool description, instructions for use, and maximum torques.
Tappex Performance data of Inserts for Plastics in generic applications.
Tappex Performance data of Inserts for Plastics in generic applications.
Installing Brass Threaded Inserts Into Nylon Using The Tappex Automatic Screwdriver & Flexiarm
In this video we demonstrate the ease at which the Tappex Trisert, brass threaded inserts, can be inserted into nylon using Tappex’s Hand Tool.
No Video? Click the cookies icon below and accept cookies
Installing Brass Threaded Inserts Into Nylon Using The Tappex Automatic Screwdriver & Flexiarm
In this video we demonstrate the Tappex 1100rpm Auto Reverse Pneumatic Screwdriver & FlexiArm and the ease with which it can be used to install Tappex Triserts, one of our brass threaded inserts, into 30% glass filled nylon.
Installing Brass Threaded Inserts Into Nylon using the Tappex flexiarm
In this video we demonstrate the Tappex 510rpm Manual Reverse Pneumatic Screwdriver & Flexiarm and show how easy it is to install Tappex’s Trisert (one of our brass self threading inserts) into 30% glass filled nylon.